Useful Safety Data Sheet Management Tips & Tricks to Try in 2024
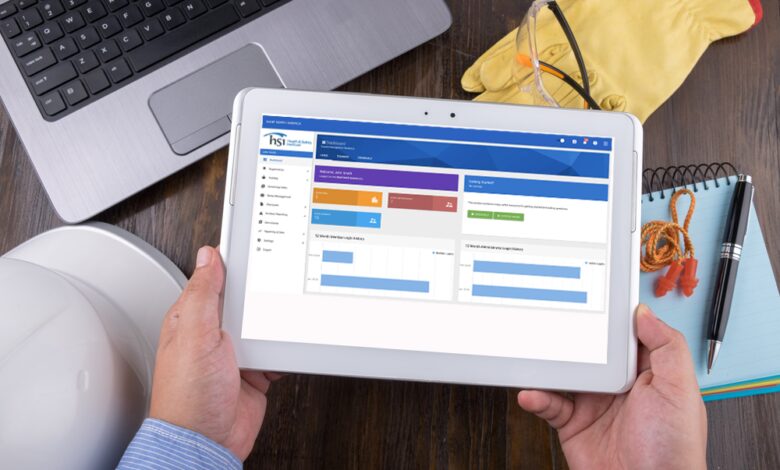
Starting this article with a short explanation for those that do not know what safety data sheet is would be good. In short terms, it is a type of informational document that importers and manufacturers prepare. They will try to cover as much information as possible about the physical and chemical properties of the products they are selling.
The details people can find there are various. For starters, it says more information about the ingredients or features of every product. Despite that, it shares more information about the manufacturer or supplier as well.
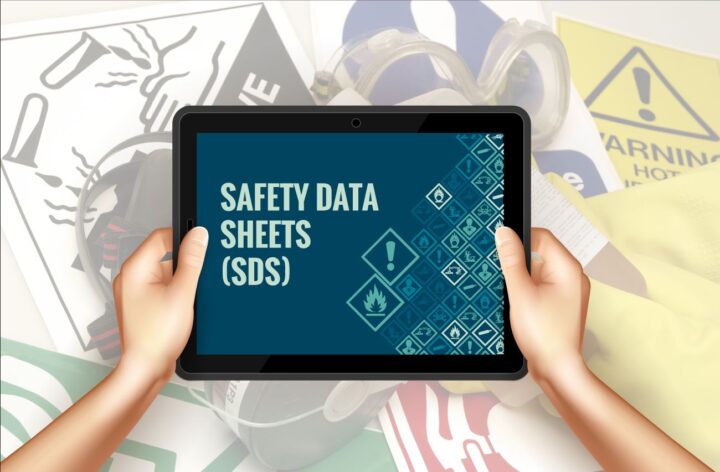
However, it does not only list the features that a product contains. It talks about the hazardous effects that the product can potentially have. For example, it describes the explosive as well as flammability properties of the product. Despite that, people that using or working with products also need to know the influence it has on their health.
However, the document itself is not just informal as it does not only share the data we mentioned. It primarily describes the prevention that people should follow in order to remain safe. Finally, the document also describes what people should do and how they should respond if something bad happens.
Anyway, the question you probably have now is whether everyone needs to have a safety data sheet. The answer to that question is “no”. It is only mandatory for those businesses that work with the so-called hazardous products.
Things are probably more clear now. Yet, something that bothers most entrepreneurs is the fact that they do not know how to manage safety data sheet properly. That is the reason why we decided to share a couple of tips with you that will help you complete this part of the job easily. Let’s find out those tips and tricks together!
First Step: Learn and Assign
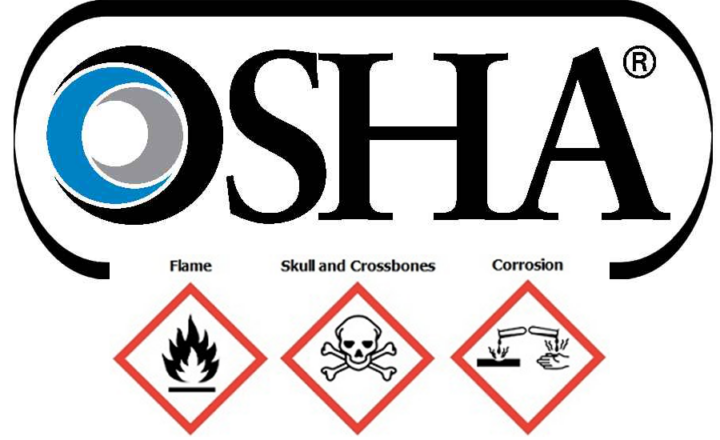
Well, before you even start the entire process, the first thing you need to do is to improve your knowledge. More precisely, you will have to get familiar with the so-called Hazard Communication Standard by OSHA. After you determine the provisions of these standards, you will easily determine what is necessary for workplace compliance. If you improve your knowledge properly, it will be much easier to manage your safety data sheet.
After you do that, the next task that you have is to assign primary responsibility to someone. The person you choose will coordinate the implementation of the hazard communication program. That program will not only address all the necessary components; it will also describe and develop the necessary training that employees need to pass through.
Now, Prepare and Implement Everything
After you complete the first step, the next thing you need to do is to get a pencil and a piece of paper and a bit of creativity. Your task will be to develop the hazard communication for labels. However, the same communication is not only limited to labels; it also covers all the forms of warning, employee information, and training that you will address in your company.
You will have to use the chemical identifier (so-called CAS) to prepare the list of hazardous chemicals properly. That will help you track the status of all the SDSs without extreme effort for all the chemicals that you are working with and can potentially be hazardous.
Work on Labels After That
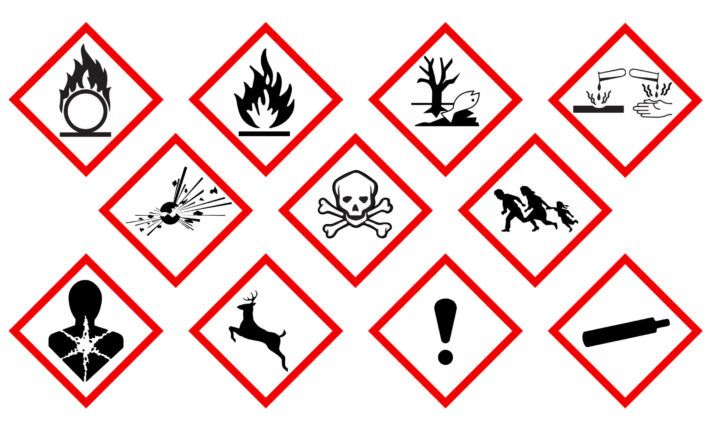
Every entrepreneur or a responsible person needs to know what the label needs to contain exactly. When you place them on the shipping containers, keep in mind that the label needs to contain the chemical identified, signal word as well as pictograms.
Unfortunately for you, the list of information is not that short as there are many more details you will need to place there. For starters, there are two statements you need to write down – precautionary and hazard statements. You will also need to give more information about the responsible parties. It is going to be enough to share the name of that person/business, address, and phone number.
So, are these pieces of information all mandatory? Well, let’s say that those containers that contain hazardous chemicals need to have at least the chemical identifier as well as general information about the chemical. However, that is only a minimum that you can provide.
Here Comes the Most Important Step: Maintenance
For starters, it may happen that this part of the job is going to be time-consuming and annoying. However, not doing it properly can cost you and someone else a lot. That is the reason why your task is to share all the mentioned information for each chemical you are working with. The excuse, in this case, does not exist.
However, writing down all the information is not going to be enough. You need to find the best possible communication channels to reach all the employees that are working in the particular work areas. Yet, the safety data list will always require changes as the laws are constantly changing. That is the reason why many people consider this part of the job time-consuming.
The good news for all the people is that they can find some useful tips as well as software that will make this task a lot easier. You can check out devibfabriek.nl after reading this article and check out how you can complete this part of the job easily. We are pretty sure you will like what you see there.
Final Thought
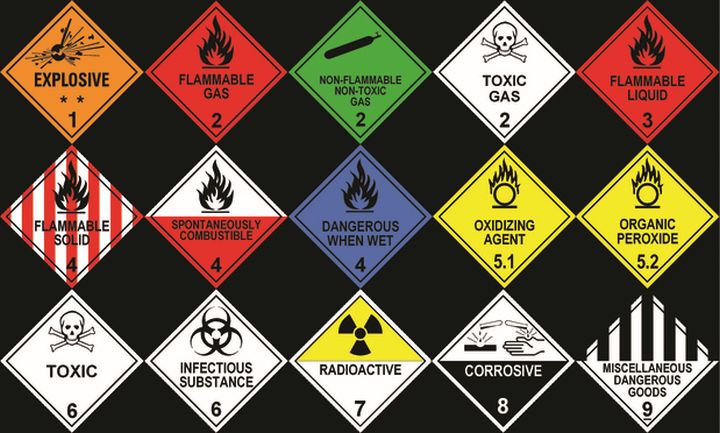
The entire process is going to be much easier in case you apply the tips we shared in this article. All you will have to do after completing these four steps is to train your workers. More precisely, you need to help them follow the latest law changes, and understand more details about hazardous chemicals. Logically, it is also essential to properly explain how they can access the safety data sheets.
You will have to check out the hazard communication program from time to time. It is essential to know at every moment whether the program is up to date or not. However, the software that we mentioned can speed up the process a lot. That is the reason why you can consider it as a good alternative!